Передовыми направлениями ресурсосберегающих технологий являются применение в машиностроении биметаллов, металлополимерных и композиционных материалов.
Использование биметаллов и металлополимерных композиций обеспечивает детапям комплекс свойств, необходимых в процессе эксплуатации, продлевает ресурс работы, экономит цветные металлы. Существует несколько способов получения биметаллов, сущность которых определяется физико-химическими процессами, вызывающими образование неразъемных соединений металлов. Среди них совместная деформация металлов в горячем и холодном состоянии, диффузионная сварка, наплавка, напыление, сварка взрывом, ультразвуком, трением и др., а также новые литейные технологии.
Проведенные авторами исследования показывают большую перспективность метода получения биметаллических заготовок путем соединения жидкофазных компонентов в процессе непрерывной разливки, что обеспечивает более прочное соединение компонентов биметалла по всей площади контакта. С разработкой теоретических и технологических основ соединения жидкофазных компонентов в процессе непрерывного литья появится научная база для создания принципиально новой технологии получения биметаллических заготовок. Это оригинальная технология в сравнении с существующими будет обладать рядом преимуществ: простотой, высокой производительностью, стабильностью качества. Она позволит производить сортовые биметаллические заготовки для широкого класса изделий.
К числу принципиально новых следует отнести технологии получения биметаллических заготовок различной теплообменной арматуры, почвообрабатывающих деталей и различных втулок из чугунов, бронз, латуней, алюминиевых сплавов, биметаллических блоков двигателей.
Для получения биметаллических заготовок испарительной арматуры холодильников и теплообменных аппаратов для конденсации серной кислоты предусматривают намораживание на трубную заготовку различных сплавов, препятствующих насыщению углеродом материала арматуры (первый случай) и защищающих от коррозионного воздействия среды (второй случай). В первом случае намораживают сталь, легированную кремнием, в дуговой печи ДСН-3, а во втором — ферросилид, содержащий ~ 14 % Si, в индукционной печи типа ИСТ-0,16. Установлена идентичность характера зависимостей δСЛ =f(τ)ΔT (±10 °С) и определены параметры, обеспечивающие формирование сплошного слоя толщиной 3… 5 мм по всей поверхности заготовки.
Особенности кристаллизации расплава при намораживании его на твердую заготовку позволяют существенно повысить качество отливки, управлять структурой сплава, уровнем физических и механических и специальных свойств. Разнотолщинность намороженного слоя — 10…20 % на длину ~ 1 м.
Влияние способа получения биметаллических заготовок на их механические свойства
Сплав | Способ получения | Свойства | |||
σв, МПа | δ,% | НВ | ρ, кг/см3 | ||
Бр05Ц5С5 | Намораживание | 270…300 | 30…37 | 70…75 | 9,2…9,3 |
Кокиль | 180 | 41 | 60 | 8,8 | |
Прокат | 320…440 | 0…16 | 60…65 | 9,0…9,1 | |
БрОЮС2НЗ | Намораживание | 350…380 | 14,6…19,8 | 116 | 9,2…9,3 |
Под давлением | 320 | 14…18 | 110 | 8,8…9,0 | |
БрОЮФ1 | Намораживание | 320…330 | 18…23 | 95… 107 | 9,2…9,3 |
Кокиль | 250 | 3 | 90 | 8,8 | |
Прокат | 250…350 | 20 | 90…120 | 8,6…8,76 | |
БрА9ЖЗ | Намораживание | 500…550 | 33…36 | 90…95 | 8,6 |
Кокиль | 500 | 12 | 100 | — | |
Прокат | 550 | 15 | 110…180 | 7,5 | |
ЛЦ40С | Намораживание | 350…450 | 30…50 | 100…120 | 9,1 |
Кокиль | 220 | 20 | 80 | — | |
Прокат | 400…500 | 5…25 | 80…130 | 8,5 |
Анализ литературы по процессу намораживания из различных сплавов на основе Fe-C, Fe-C-Si, Cu-Al-Fe, Cu-Sn и других систем позволяет сделать вывод, что намораживание целесообразно использовать для равностенных отливок с толщиной стенки 1,5…25 мм предпочтительно симметричной конструкции, а сам процесс рационально производить в плавильных агрегатах с регулированием температуры расплава.
Условия армирования отливки при литье методом направленного затвердевания обеспечивают равномерность структуры и свойств по высоте и периметру заготовки, однако определяют и различную скорость затвердевания и, соответственно, неоднородность структуры в поперечном сечении.
Актуальными являются работы по созданию и использованию технологий, связанных с утилизацией и переработкой отходов черных и цветных металлов, а также применению в машиностроении изделий из композиционных материалов и биметаллов взамен традиционно используемых цветных металлов и сплавов. Часть этих проблем может быть решена в рамках развития технологии вертикального и горизонтального непрерывного литья. Из всех видов литейных технологий процессы непрерывного литья наиболее полно отвечают современным требованиям экологической чистоты, ресурсосбережения и качества отливок.
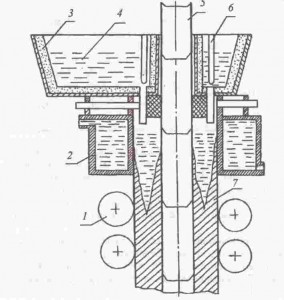
Создание установок горизонтального типа позволяет решать целый ряд экономических и организационных проблем:
- снижение капитальных затрат;
- возможность размещения установок в действующих цехах, так как для их размещения не требуется строительства колодцев и башен;
- уменьшение эксплуатационных затрат благодаря удобству обслуживания, так как все оборудование расположено на уровне пола цеха;
- возможность совмещения установки непрерывной разливки с прокатным станом;
- возможность получения армированных и биметаллических заготовок.
Использование стальной проволоки или сетки для армирования чугунных профильных заготовок дает возможность получать отливки из серого чугуна, механические свойства которых не уступают свойствам легированных чугунов и высокоуглеродистых сталей.
Высокими темпами продолжает развиваться непрерывная разливка стали. В СНГ в настоящее время эксплуатируется более 50 установок непрерывной разливки стали общей проектной мощностью более 10 млн. т в год. Освоена технология разливки более 250 марок стали. По отечественным и зарубежным данным машины непрерывного литья заготовок позволяют улучшить условия труда в сталелитейных цехах, повысить производительность в сталелитейных и прокатных цехах и обеспечить высокий выход годного продукта (95…97 %).
Для управления затвердеванием крупных отливок и массивных профильных заготовок используется интенсивное охлаждение слитка в кристаллизаторе, применяют внутренние холодильники (арматура) и организуют вторичное охлаждение.
Качество получаемых слитков и стабильность условий формирования заготовки в кристаллизаторе характеризуется относительным постоянством теплоотвода, который определяется постоянством таких параметров, как скорость разливки, состав и толщина слоя шлакообразующей смеси, температура разливки, химический состав стали и др.
Наиболее существенной по своему влиянию является скорость разливки v, определяющая величину теплоотвода при заданном сечении и высоте кристаллизатора, толщину затвердевшей корки на выходе из кристаллизатора, уровень термических напряжений в формирующейся оболочке слитка.
Для таких деталей химической аппаратуры как корпуса аппаратов, патрубки, трубы, фланцы и других, работающих в коррозионных средах, целесообразно использовать двухслойные стали и сплавы. Листовые двухслойные стали состоят из основного слоя — низколегированной (16ГС, 09Г2, 20Х, 12ХМ, 09Г2С и др.) или нелегированной углеродистой стали и коррозионно-стойкого плакирующего слоя толщиной 2…6 мм из сталей 08Х18Н10Т, 06ХН28МДТ, 10Х17Н13М2Т или никелевых сложнолегированных сплавов.
Для эффективного направленного затвердевания и торможения развития ликвационных процессов в массивных отливках и слитках из легированных износостойких сталей типа 1 ЮГ 13Л, 10Х12НДЛ, 15Х14НЛ, 120Г10ФЛ устанавливаются холодильники из хромоникелевых сталей. Прочностные свойства сталей для холодильников должны быть выше, чем у матричного металла отливки. Состав контактной зоны при использовании хромоникелевых холодильников для высоколегированных марганцевых сталей приведен на рисунке.
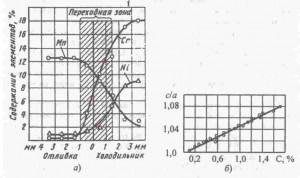
При непрерывном литье машиностроительных профилей эффективно применять армирование дисперсными частицами и волокнами.
Использование биметаллических профильных заготовок и армированных отливок постоянно расширяется; за рубежом применяют заготовки, полученные способом армирования композиционных материалов волокнистым графитом.
Схемы армирования отливок при литье под давлением при установке арматуры перпендикулярно плоскости разъема формы показаны на рисунке; в Японии их используют также при сборке велосипедных рам на вертикальных машинах с усилием прессования 120 кН. На рисунке дан пример типичного литого узла армированной детали из трех элементов — изогнутой тонкостенной трубы из алюминия, ступенчатого вала с фигурным выступом из титанового сплава и собственно отливка. При изготовлении этого узла пайкой значительно повышается трудоемкость работ и себестоимость продукции. Примеры применения арматуры на крупных отливках типа шабот массой 25 т приведены на рисунке. Конструкции пресс-форм для получения армированных отливок приведены на рисунке.
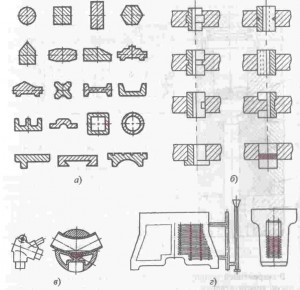
Тяжелые условия эксплуатации машин (высокий вакуум, низкие или высокие температуры, агрессивные среды и т.д.) предъявляют к материалам особые требования. Для удовлетворения этих требований создано много сплавов на основе различных металлов, а также композиций на основе металлов и неметалл.
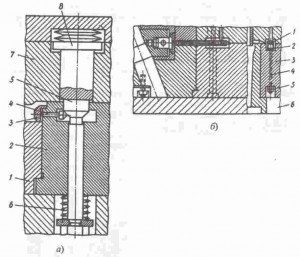
В современной технике широко применяют стали, обеспечивающие высокую конструктивную прочность, и сплавы, которые остаются прочными при высоких температурах, вязкими при температурах, близких к абсолютному нулю; они обладают высокой коррозионной стойкостью в агрессивных средах. Классификация таких сплавов представлена на рисунке.
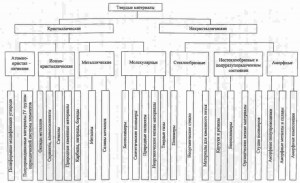
Кристаллические материалы по типу связи между частицами подразделяют на атомные, ионные, металлические и молекулярные. Из атомно-кристаллических материалов наибольшее значение в технике имеют полиморфные модификации углерода (алмаз, графит и др.) и полупроводниковые материалы на основе IV группы периодической системы элементов.
Углеродные волокна — новый вид волокнистых материалов, выпуск которых в промышленных масштабах освоен лишь в последние годы. Наиболее распространенный способ их получения освоен на термической обработке различных органических волокон в строго контролируемых заданных температурно-временных режимах и средах. Исходное сырье — различные химические волокна, полученные из полимерных органических соединений, главным образом целлюлозные и полиакрилонитрильные.
В Институте общей и неорганической химии НАН Беларуси разработана новая группа волокон — химически модифицированные углеродные волокна, содержащие в своей структуре металлы, а также остатки различных кислот и оснований. Наряду с комплексом ценных свойств, характерных для известных углеродных материалов, они обладают также заданной химической и сорбционной активностью, что позволяет получать композиционные материалы принципиально новым способом и с новыми свойствами.
В последние годы созданы различные градиентные материалы с использованием меди, углеграфитовых добавок и других, которые могут быть использованы для кристаллизаторов при непрерывном литье.
Характерной особенностью существующих методов непрерывного литья биметаллических заготовок является плакирование твердой основы жидким металлом, что делает проблематичным получение требуемых плотности и сплошности контакта между компонентами. Для более качественного соединения составляющим применяют различные технологические приемы, связанные в основном с подготовкой поверхности плакируемого металла, что ведет к дополнительным затратам и удорожанию производимой продукции. Предложен принципиально новый способ получения биметаллических заготовок, в котором соединение компонентов происходит в жидкофазном состоянии, без перемешивания.
Для производства прямоугольных двухслойных заготовок методом непрерывного горизонтального литья разработана схема, где разделительным элементом является пластина. Расплавы металлов 7 и 2 заливают в металлоприемник 3, разделенный на две секции. Металл 2 через канал 7, образуемый графитовой вставкой 8 и пластиной 6, подается в верхнюю часть, а металл 1 через канал 4, образуемый пластиной 6 и графитовой вставкой 5, подается в нижнюю часть формирующейся в кристаллизаторе 9 биметаллической отливки 11 (12). Полученную плоскую биметаллическую отливку циклически (движение-остановка) вытягивают при помощи валков 13. Конструкция кристаллизатора обеспечивает отвод тепла преимущественно через верхнюю и нижнюю поверхности формирующейся в кристаллизаторе биметаллической отливки.
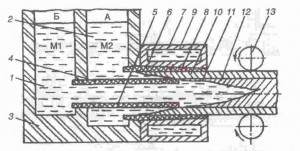
По мере извлечения биметаллической отливки 11 происходит рост корки полой заготовки металла периферии. При выходе образовавшейся заготовки из зоны, ограниченной протяженностью металлопровода 3, внутренняя поверхность корки входит в контакт с жидким металлом 7, после чего начинается процесс формирования биметаллической отливки 77. На первом этапе происходит образование переходной зоны двух металлов, на втором — затвердевание корки металла 2.
При оптимальном режиме вытягивания слитка толщина корки 9 на торце металлопровода 3 в конце времени остановки должна быть равна ширине кольцевого канала 4. В этом случае при продвижении отливки на один шаг между металлопроводом и заготовкой будет возникать зазор, величина которого будет определять количество жидкой фазы металла 2, а следовательно, и ширину переходной зоны, образуемую жидкими фазами обоих металлов.
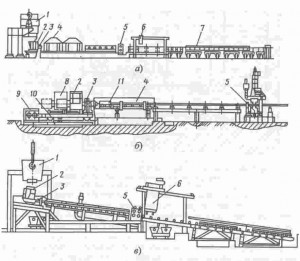
В настоящее время в различных странах работает несколько типов горизонтальных У НРС. Высокое качество заготовок позволяет получать УНРС с устройством для электромагнитного перемешивания.
К основным задачам автоматизации работы УНРС относятся;
- контроль, регулирование и стабилизация уровня металла в промежуточном ковше;
- организация охлаждения слитка в кристаллизаторе и в зоне вторичного охлаждения;
- резка заготовок на мерные длины и маркировка.
Схема автоматического управления процессом непрерывной разливки ВНИИЧермета им. Бардина представлена на рисунке. Для определения уровня металла в промежуточном ковше применяют тензометрические датчики (месдозы). В качестве датчиков уровня металла в кристаллизаторе чаще всего используют радиоизотопный метод.
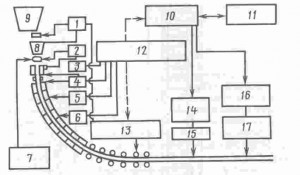
Для предотвращения прилипания корочки слитка к кристаллизатору и возможного при этом зависания слитка (и образования трещин) при помощи механизмов качания организуют непрерывное возвратно поступательное движение кристаллизатора. Для того чтобы избежать появления па поверхности слитка грубых складок (следов качания), интенсивность качания должна быть очень высокой (на современных УНРС до 400 и более раз в минуту).
На автоматизированных УНРС освоено производство ряда сложнолегированных износостойких сталей, включая высокопрочные стали с мелкозернистой структурой и различной кристаллической решеткой.
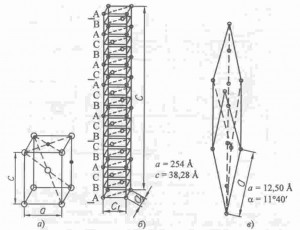