Фрикционные фосфористые чугуны относятся к широко распространенным конструкционным материалам, используемым для изготовления деталей тормозных устройств, механизмов сцепления, фрикционных и других механизмов трения.
Основными отличительными особенностями фрикционных чугунов являются: высокий коэффициент трения, высокая износостойкость и способность противостоять образованию задиров в большом интервале температур, повышающихся на поверхности трения.
Этим требованиям удовлетворительно отвечают серые фосфористые чугуны с металлической основой из мелкозернистого перлита с равномерно распределенными включениями двойной и частично тройной фосфидной эвтектики и пластинчатого графита. Первичной структуре принадлежит решающее значение в формировании свойств фрикционных чугунов.
В чугунах с углеродным эквивалентом Сэ более 5,2 в отливках при малых скоростях охлаждения образуется розеточная форма графита, что оказывает отрицательное влияние на механические и эксплуатационные свойства фрикционных изделий. При этой форме графита в центральной зоне образцов диаметром 30…60 мм образуется преимущественно феррит при литье в песчано-глинистые формы, что приводит к снижению прочности чугуна, вибростойкости и износостойкости. Поэтому для повышения прочностных свойств и износостойкости фосфористых чугунов при изготовлении фрикционных толстостенных отливок из заэвтектических чугунов должны выдерживаться соотношения Si / С = 0,65 и Si / (С + N) ≥ 0,65.
Более высокие механические свойства обеспечивают чугуны доэвтектического и эвтектического состава. В отливках с толщиной стенок 40 мм при повышенном содержании фосфора получается металлическая основа П96 (Ф4) — ЭФЗ — ПД0,5 — ФЭп 2000 и графит ПГ6 — ПГрЗ — ПГд45 — ПГф2, которые обеспечивают литым изделиям фрикционно-износные свойства при работе в паре с асбофрикционными материалами.
Если в бинарной Fe-C-системе критическая скорость кристаллизации, при которой серый чугун переходит в белый, равна 420…450 мкм/гс, то в тройной Fe-C-P-системе она изменяется от 30 до 100 мкм/гс. Это является одной из причин получения структуры белого чугуна с повышенной концентрацией цементита.
Изменение длины включений графита чугуна в основном определяется условиями охлаждения и размером отлитого образца. Чисто перлитная структура в массивных образцах обеспечивается только при относительно низкой степени эвтектичности Sэ = 0,7…0,8, что характерно для фосфористых нелегированных и немодифицированных чугунов, используемых для производства тонкостенных фрикционных отливок. При увеличении степени эвтектичности до 0,8…0,9 количество феррита в структуре резко возрастает, а износостойкость образцов снижается.
На рисунке приведены данные по изменению износа (а) и твердости (б) образцов из чугунов с разной степенью эвтектичности, отлитых в песчано-глинистую форму 1 и кокиль 2. При литье в песчано-глинистую форму длина включений графита в отливках мало зависит от степени эвтектичности чугуна, а количество перлита снижается при увеличении степени эвтектичности чугуна с 0,7 до 0,9. Временное сопротивление чугуна при этом снижается с 276…281 до 198…226 МПа, в то же время как при литье в кокиль изменение временного сопротивления при изменении степени эвтектичности чугуна с 0,7 до 0,9 не превышало 7… 11 %.
При увеличении содержания фосфора в этих чугунах повышается коэффициент трения и другие фрикционно-износные характеристики в условиях сухого трения по стали. На рисунке приведены данные о величине коэффициента трения фосфористых чугунов, содержащих 0,12…1,18 % фосфора при давлении 1,05 МПа и различных скоростях скольжения. Номинальная площадь соприкосновения испытуемого образца с диском была постоянной, а скорость скольжения колебалась от 1 до 16 м/с; с увеличением скорости скольжения коэффициент трения снижается.
На рисунке, б видно, что твердость чугуна существенно зависит от его степени эвтектичности, а ее значения наиболее низкие в образцах, отлитых в песчано-глинистую форму. При высоких скоростях охлаждения на установках непрерывного литья твердость значительно повышается. Для определения фрикционно-износных характеристик использовали машины трения МИ-1М, ИМ-58, СМЦ-2, И47-К54идр.
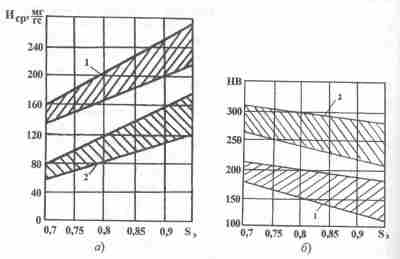

В таблице приведены данные о влиянии содержания фосфора на износ при сухом трении, термическую стойкость и твердость чугуна в литом состоянии. Эти данные получены с использованием в качестве контртела закаленных стальных образцов, асбофрикционных материалов марок 6КХ-1Б, НФС-1 и ретинакса марки ФК-16л. Нагрузка при испытании увеличивалась после стабилизации момента силы трения, исходя из которого рассчитывался коэффициент трения:
где Р — нагрузка; r — радиус ролика; i — число пар трения; Мтр — момент силы трения.
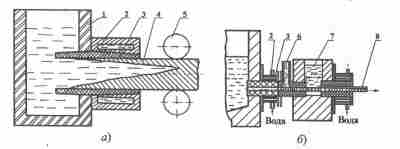
Увеличение коэффициента трения, % | Характеристики износостойкости при трении без смазки | |||||
Содержание фосфора в чугуне % (мае.) | Твердость чугуна в отливках НВ | Скорость изнашивания в процессе приработки, м км/гс | Износ при торцовом трении на машине И47-К54, мг/гс | Относительная износостойкость при трении качения со скольжением, % | Термическая стойкость, циклы | |
0,06 | 100 | 172 | 16,0… 18,6 | 260 | 100 | 140 |
0,12 | 112 | 180 | 13,0… 14,4 | 182 | 114 | 132 |
0,18 | 122 | 189 | 10,6… 11,2 | 166 | 118 | 126 |
0,30 | 128 | 196 | 8,8…10,4 | 149 | 132 | 114 |
0,55 | 132 | 218 | 7,5…8,7 | 132 | 144 | 86 |
0,96 | 138 | 225 | 7,0…7,8 | 116 | 156 | 73 |
1,35 | 144 | 233 | 6,2…7,2 | 108 | 165 | 62 |
1,85 | 148 | 241 | 5,6…6,7 | 85 | 178 | 36 |
Испытания проводились в стационарном режиме при постоянном коэффициенте трения 0,30…0,35. В качестве базового состава использовался чугун, содержащий 0,06 % фосфора, имеющий степень эвтектичности 0,75 и твердость в литом состоянии 172 НВ.
Относительная износостойкость фосфористых фрикционных чугунов
где Иэ — износ эталона; И0 — износ испытуемого образца.
Термическая стойкость оценивалась количеством циклов нагрева до 800 °С и охлаждения на воздухе до появления трещины.
Установлено, что добавка фосфора в серый чугун повышает его фрикционные свойства, но способствует образованию трещин, снижает термическую стойкость, стабильность коэффициентов трения при повышенных температурах и механические свойства, особенно динамическую прочность. Для улучшения механических свойств фрикционного серого чугуна целесообразно реализовать в нем хотя бы ограниченную пластичность, предотвращающую его хрупкое разрушение в отливках. При увеличении степени эвтектичности фосфористых чугунов до 0,8… 1,0 имеет место значительное снижение пластичности, хотя дисперсность перлита остается достаточно высокой как при литье в кокиль, так и в песчано-глинистыми формы. В отливках с толщиной стенок более 30 мм возникает осевая пористость и неоднородность структуры. В отливках с толщиной стенок 16…20 мм при литье в кокиль получается структура отбеленного чугуна при SЭ > 0,75.
Переход от структуры серого чугуна к структуре белого чугуна в системе железо-углерод-фосфор происходит при более низких скоростях охлаждения. Сравнивая структуры эвтектики, полученные при одинаковых скоростях кристаллизации, определяем, что тройная эвтектика оказывается значительно мельче, чем двойная, и это указывает на более высокую степень переохлаждения при кристаллизации железо-углерод- фосфидной эвтектики.
Чтобы в исследованиях различить Fe3C и Fe3P, травление образцов нужно производить реактивом Мураками, который окрашивает Fe3P в коричневый цвет.
Для работы в фрикционных парах, в которых контактирующие поверхности нагреваются незначительно и опасности образования трещин нет, содержание фосфора в чугуне может достигать 1,35… 1,85 %. Однако для изготовления ряда фрикционных изделий, работающих при повышенных температурах и ударных нагрузках, когда одновременно с высокой износостойкостью необходимы повышенная термическая стойкость и динамическая прочность (например, для тормозных барабанов, в металле которых возможно образование трещин), необходимы более термостойкие чугуны и другие фрикционные сплавы.
Для получения серых фрикционных чугунов наряду с легированием фосфором используются комплексные лигатуры и модификаторы, содержащие дибориды тугоплавких металлов, дисульфиды молибдена, нитриды бора и редкоземельных металлов и другие компоненты, снижающие износ при сухом трении и повышающие коэффициент трения. Установлено, что фрикционные материалы с диборидами тугоплавких металлов и нитридами бора обеспечивают стабильный коэффициент трения, хорошо прирабатываются к контрэлементу, не схватываются с ним, являются коррозионно-стойкими, негорючими, обладают необходимой механической прочностью, износостойкостью, а в ряде случаев и высокими упругопластическими свойствами.
Для фрикционных изделий, в процессе эксплуатации нагревающихся до температур 200…500 °С, более эффективными конструкционными материалами являются микролегированные серые чугуны, содержащие не более 0,15 % фосфора.
В таблице приведены данные о влиянии ряда легирующих элементов на твердость и величину износа при сухом трении фрикционных отливок с толщиной стенок 30…40 мм.
На первичную кристаллизацию чугуна и износостойкость влияют температурные режимы плавки, внепечной обработки, разливки, а также количество и состав неметаллических включений и примесей; они определяют как выделение и рост графита, так и структуру металлической основы, механические и эксплуатационные свойства чугуна в отливках. На практике для контроля качества фосфористого чугуна отливают в песчаные литейные формы технологические пробы с размерами квадратного сечения 25 х 25 мм или диаметром 35 мм и длиной 120 мм. Экспресс-контроль проводят по виду излома технологической пробы.
Практический интерес представляет технология производства отливок из износостойкого доэвтекического чугуна Fe-C-Si-P с его заливкой в форму с перегревом 100…250° и скоростью охлаждения от 1,8 до 4 К/с до температуры ликвидуса.
Влияние микролегирования на твердость и износостойкость серых фрикционных чугунов
Твердость НВ | Снижение износа, % | Относительная стабильность коэффициента трения, % | Присадка микролегирующих добавок, % (мае.) | ||||||
Мо | Cr | Cu | Ni | V | Sb | В | |||
178 | 3,0 | 122 | — | 0,23 | — | — | — | — | — |
182 | 5,1 | 128 | — | — | 0,15 | — | — | — | |
186 | 7,8 | 136 | 0,12 | — | — | — | — | ||
190 | 10,2 | 132 | — | 0,17 | — | — | |||
195 | 12,5 | 138 | — | 0,23 | — | ||||
202 | 15,1 | 146 | — | — | 0,35 | ||||
207 | 17,0 | 130 | 0,55 | — | |||||
212 | 20,2 | 155 | 0,12 | — | 0,17 | ||||
221 | 25,3 | 156 | 0,23 | 0,55 | — | ||||
228 | 30,0 | 158 | 0,15 | 0,23 | |||||
235 | 35,7 | 162 | — | 0,17 | 0,35 | ||||
241 | 43,2 | 170 | 0,12 | 0,55 | — | 0,23 | |||
248 | 50,5 | 184 | 0,47 | — | — | 0,35 | |||
256 | 58,0 | 188 | 0,50 | — | 0,27 | 0,17 | |||
264 | 60,5 | 192 | 0,50 | — | 0,17 | 0,23 |
Примечание. В качестве эталона использовался нелегированный фосфористый чугун твердостью 172 НВ, стабильность коэффициента трения которого условно принята за 100 %. Расплав получен в индукционной печи и заливался в формы при 1336… 1350 °С.
На рисунке показана зависимость температур ликвидуса Тл, эвтектического переохлаждения АТЭ и свойств от степени эвтектичности S3 фосфористых (0,1…0,16 % Р) чугунов доэвтектического состава. Твердость, структура, износостойкость и другие свойства, зависящие от степени эвтектичности чугуна, могут быть определены по эвтектическому переохлаждению и температуре ликвидуса, регистрируемые при термическом анализе Fe-C-Si-P-расплава.
В таблице показано влияние состава такого чугуна на его структуру и твердость. При этом следует отметить, что у чугунов, микролегированных РЗМ в количестве от 0,03 до 0,16 % (мас.), эвтектическое переохлаждения ΔТэ больше, чем у чугунов без РЗМ (составы 1 и 5), и соответственно твердость ниже.
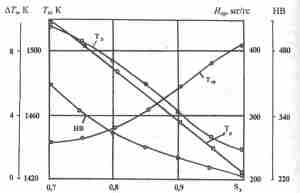
Снижение температуры эвтектического превращения при кристаллизации отмечено при микролегировании чугуна (состав 10), что показано на рисунке.
В случае состава 10 увеличение длины вертикального участка на термической кривой усадки указывает на образование большего количества эвтектики и мелкозернистой структуры. Повышение угла наклона кривой усадки на участке расширения связано с увеличением количества центров кристаллизации в расплаве. В пробах из чугунов, крутизна кривых усадки которых больше, структура более мелкозернистая, а твердость и износостойкость выше. Установлено, что на угол наклона кривых усадки на участке расширения оказывают влияние не только основные элементы и микролегирующие добавки, но и технологические примеси: сера, кислород, азот и др. Например, повышение в чугуне содержания серы с 0,006 до 0,1 % (мас.) увеличивает крутизну кривой усадки на 12°, а увеличение содержания азота с 0,003 до 0,008 % (мас.) — на 7°. Это связано с тем, что сера и азот образуют в расплавах зародыши, служащие центрами кристаллизации, которые оказывают влияние на структуру чугуна в отливках.
Влияние химического состава на структуру и твердость фрикционных чугунов
№ состава | Содержание компонентов, % (мае.) | Структура чугуна | ||||||||
С | Si | Mn | Р | РЗМ | В | S | N | Твердость НВ | ||
1 | 3,53 | 2,42 | 0,12 | 0,08 I | — | — | 0,02 1 | П50, Ф50 | 181…193 | |
2 | 3,53 | 2,42 | 0,12 | 0,08 | 0,03 | — | — 1 | П70, ФЗО | 187…201 | |
3 | 3,52 | 2,43 | 0,12 | 0,08 | 0,07 | . —, | — | П80, Ф20 | 221…235 | |
4 | 3,51 | 2,45 | 0,12 | 0,07 | 0,16′ | — | — | П100 | 241…255 | |
5 | 3,28 | 2,12 | 0,16 | 0,16 | 0,03 | — | 0,02 | П75, Ф20, Л5 | 217…227 | |
6 | 3,28 | 2,12 | 0,16 | 0,16 | — | — | П85, Ф15, Л5 | 225…237 | ||
7 | 3,27 | 2,13 | 0,16 | 0,16 | 0,08 | — | П90,Л10 | 235…250 | ||
8 | 3,25 | 2,15 | 0,15 | 0,16 | 0,16 | — | П70, ЛЗО | 255…272 | ||
9 | 3,33 | 2,47 | 0,24 | 0,12 | — | 0,02 | 0,005 | П80, Л20 | 218…228 | |
10 | 3,32 | 2,52 | 0,23 | 0,11 | 1 | 0,03 | 0,02 | 0,006 | П85.Ф15 | 227…235 |
Обозначения: П — перлит; Ф — феррит; Л — ледебурит.
Тормозные колодки и другие фрикционные отливки из таких чугунов обычно получают в песчано-глинистых формах и термической обработке не подвергают. При литье в металлические формы в чугуне повышают содержание кремния до 2,3…2,5 %. При получении в структуре междендритного графита используют термообработку.
Проблема получения чугунных кокильных отливок без аномальной ферритно-графитовой структуры до настоящего времени полностью не решена. Значительная часть тонкостенных кокильных отливок, полученных без отбела, содержит в структуре на ферритной основе междендритный дисперсный графит, что резко снижает их эксплуатационные свойства, особенно износостойкость.
Режим упрочняющей термической обработки и, в частности, температуру нагрева для чугуна с междендритным графитом (кокильное литье) необходимо выбирать с учетом особенностей исходной структуры чугуна и ее изменения в процессе нагрева. Температура аустенизации чугуна с междендритным графитом должна назначаться не на 30…50 °С выше Ак1 как для обычных серых чугунов с пластинчатым графитом, а на 100… 150 °С выше Ак1
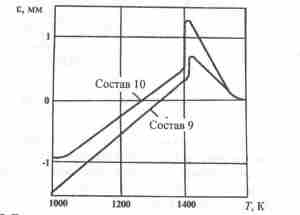
Модифицирование доэвтектических износостойких чугунов редкоземельными металлами в количестве 0,03…0,16 % (мас.) снижает точки первичных и эвтектических превращений, увеличивает эвтектическое переохлаждение, измельчая структуру чугуна и повышая твердость и износостойкость. В чугунах, состав которых близок к эвтектическому, эвтектическое переохлаждение незначительное и установление связи между данными термического анализа и свойствами чугуна затрудняется.
Метод контроля качества расплава по кривым охлаждения и усадки чугунов по длительности не превышает 3 гс и позволяет проводить корректировку химического состава и состояния расплава, выплавленного в дуговой или индукционной печи, перед разливкой в литейные формы, а в ряде случаев и в ковше.
Коэффициент трения, пластичность и прочность серого чугуна, имеющего степень эвтектичности 0,8… 1,0, существенно повышаются при легировании молибденом в количестве 0,12…0,9 % (мас.), для нейтрализации карбидообразующего действия которого в чугун могут вводиться сурьма и никель.
Для повышения вязких свойств чугуна может использоваться комплексное легирование чугуна молибденом и медью или молибденом и никелем. Сочетание молибдена и никеля позволяет получать бейнитный чугун, обладающий одновременно высокой прочностью, вязкостью и относительно стабильным при повышении температуры коэффициентом трения.
Микролегирование серого чугуна бором обеспечивает повышение устойчивости коэффициента трения вследствие образования карбоборидов с более мелкой износостойкой твердой эвтектикой, чем фосфидная. Отливки из чугунов, микролегированных бором до 0,35 % (мас.), имеют более высокую герметичность, чем отливки из высокофосфористых чугунов. При увеличении содержания бора более 0,35 % (мас.) снижаются пластичность и трещиностойкость чугуна.
Из таблице видно, что комплексное микролегирование является эффективным методом повышения временного сопротивления и твердости отливок из фрикционных чугунов. Титан и TiN в фосфористых чугунах не используют, так как они снижают коэффициент трения.
Влияние микролегирования на твердость и прочность фрикционных чугунов
Твердость НВ | Временное сопротивление, МПа | Присадка микролегирующих элементов, % (мае.) | ||||||
Мо | Cr | Cu | Ni | Sb | V % | В | ||
172 | 197 | — | — | — | — | |||
186 | 211 | — | 0,13 | — | — | — | ||
187 | 220 | — | — | — | 0,35 | — | ||
189 | 221 | 0,12 | — | — | % | — | ||
191 | 232 | — | — | 0,17 | — | |||
193 | 232 | — | — | 0,23 | — | |||
197 | 232 | — | — | 0,35 | ||||
201 | 240 | — | 0,55 | |||||
220 | 251 | 0,23 | 0,55 | |||||
223 | 263 | 0,15 | 0,23 | |||||
227 | 272 | — | 0,17 | 0,35 | ||||
235 | 283 | 0,12 | 0,55 | — | 0,23 | |||
237 | 294 | 0,47 | 0,35 | |||||
245 | 295 | 0,50 | 0,27 | 0,17 | ||||
249 | 298 | 0,50 | 0,17 | 0,23 |
При микролегировании фосфористых фрикционных чугунов металлической сурьмой последняя вытесняет фосфор из твердых фаз в жидкий раствор, что приводит к увеличению площади включений фосфидной эвтектики. Количество цементита в отливках становится больше, что приводит к увеличению микротвердости фосфидной эвтектики и фрикционно-износных свойств отливок.
Можно предположить, что эвтектика в сплавах Fe-C-Si-P-Sb не сложная фосфидно-сурьмянистая, а обычная тройная игольчатая типа ФЭ4. Термических анализ, проведенный с помощью дифференциальной термопары, и микроанализ структуры фосфидной эвтектики с помощью микроанализатора «Микроскан-5» подтверждают это предположение.
Увеличение (при микролегировании сурьмой) площади, занимаемой отдельными включениями фосфидной эвтектики, приводит к увеличению стабильности коэффициента трения и снижению износа. Такое воздействие характерно и для хрома. Однако хром приводит к неравномерному распределению фосфидной эвтектики и расположению ее преимущественно по границам зерен в виде замкнутой сетки. При комплексном микролегировании чугуна сурьмой в количестве 0,15…0,35 % (мас.) и хромом 0,05…0,25 % (мас.) отмечается более равномерное распределение фосфидной эвтектики в отливках с толщиной стенок 30…60 мм и повышение термической стойкости чугуна. При содержании в чугуне 0,23 % (мас.) бора и 0,1 % (мас.) сурьмы твердость отливок повышается до 227 НВ, а термическая стойкость до 230 циклов.
Для получения игольчатой структуры фрикционные чугуны дополнительно легируют молибденом. При микролегировании чугуна молибденом твердость повышается до 245…320 НВ, а фрикционные свойства достигают параметров, необходимых для изготовления штампов, проводок проволочных станов и сепараторов подшипников.
Для износостойких деталей с игольчатой структурой используется комплексное легирование чугуна вольфрамом, молибденом и никелем. Поскольку такое легирование уменьшает критическую скорость закалки и увеличивает прокаливаемость, чугуны с игольчатой структурой могут быть использованы для прокатных валков и других толстостенных износостойких отливок. Под влиянием термической обработки и легирующих элементов существенно меняется природа карбидных фаз, что отражается на свойствах отливок.
При комплексном микролегировании повышается плотность чугуна в толстостенных отливках. Склонность к усадочной пористости фосфористых чугунов снижается:
- при введении бора, бария и висмута;
- при снижении температур модифицирования и заливки;
- при увеличении времени выдержки расплава после микролегирования и модифицирования;
- при уменьшении содержания в расплаве фосфора, хрома, марганца, алюминия и серы;
- при использовании просушенных песчано-глинистых литейных форм и кокилей.
Дополнительное введение в расплав кремния, кальция, циркония и углерода увеличивает склонность чугуна к усадочной пористости и снижает фрикционные свойства отливок. Изменение соотношения между фосфором, кремнием, марганцем и хромом в фосфористых чугунах является важнейшим резервом регулирования стабильности коэффициента трения и других фрикционных свойств, а присадка молибдена в количестве 0,3…0,6 % (мас.) повышает фрикционную теплостойкость и служебные свойства.
Чугуны, легированные (0,3…0,6 %) молибденом, (0,2…0,4 %) фосфором и (0,03…0,06 %) бором, обладают достаточно высокими механическими свойствами, позволяют выравнивать однородность структуры графита и металлической основы в толстостенных отливках. Они обладают достаточно высокими фрикционными свойствами и стабильным (до 600 °С) коэффициентом трения, снижают изнашивание деталей трущихся пар и могут быть рекомендованы для крупных фрикционных накладок, цилиндров и толстостенных барабанов с целью повышения их надежности при работе как при низких, так и высоких температурах. Чугуны, содержащие только фосфор и бор или фосфор и ванадий, могут быть рекомендованы только для изготовления тонкостенных отливок, работающих при температурах до 500 °С.
В фосфористом чугуне с бором длина включений графита уменьшается до 7… 15 мкм, в металлической основе отсутствует феррит, а в перлите появляются сложные карбобориды большой твердости, что повышает коэффициент трения и износостойкость. Бор относится к элементам с небольшим атомным радиусом (0,091 нм), свободно диффундирует в железо и по аналогии с азотом и углеродом образует твердый раствор типа внедрения. Бор может замещать до 80 % углерода в цементите без изменения его орторомбической решетки. В железоуглеродистых сплавах бор образует бороцементит Fe3(C,B) и фазы с кристаллическими решетками цементита, а также дисперсные нитриды BN. В высокофосфористых чугунах могут образовываться боридные фазы типа Ме3В2 и Ме3В, повышающие также устойчивость коэффициента трения и снижающие их износ при трении.
При работе в условиях отрицательных температур стабильным коэффициентом трения обладают также чугуны, микролегированные оловом, сурьмой или редкоземельными металлами.
Для перлитизации чугуна в отливках с толщиной стенки 50 мм необходимо вводить в расплав 0,10 % олова, а в отливках с толщиной стенок 80… 100 мм полностью перлитная структура достигается при содержании олова 0,20 %. Если исходный чугун кристаллизуется с образованием мелкого переохлажденного графита, то требуется использовать более значительные количества легирующих добавок для получения в отливках преимущественно перлитной структуры.
Получение перлитной структуры может быть достигнуто при совместном легировании расплава оловом и сурьмой. С добавкой сурьмы измельчается структура и повышается износостойкость серого чугуна. При увеличении содержания сурьмы в чугуне до 0,5 % повышаются механические свойства, особенно временное сопротивление при растяжении.
Временное сопротивление чугуна, содержащего 0,27…0,37 % меди и 0,08 % олова, на 10 % выше, чем чугуна, содержащего только олово или
только медь. В пробах диаметром 40 мм введение 0,55 % меди обеспечивает преимущественно перлитную структуру, обладающую высокой коррозионной стойкостью и задиростойкостью. Такой чугун хорошо работает в паре с таким материалом, как ретинакс марки ФК-16л.
Перлитная структура характерна и для фрикционных чугунов, содержащих 3,3…6,0 % алюминия и 0,18…0,5 % фосфора. В отливках из такого чугуна может содержаться различное количество легированного алюминием феррита и включений фосфидной эвтектики, которые оказывают заметное влияние на снижение износа при трении без смазки и увеличение коэффициента трения. При увеличении содержания алюминия в отливках более 6 % отмечается рост их износостойкости, прочности и коэффициента трения при повышенных температурах.
Наиболее распространены высоколегированные алюминиевые чугуны с пластинчатым графитом, которые обладают рядом ценных физических и эксплуатационных свойств: высокой коррозионной стойкостью, износостойкостью, немагнитностью, жаропрочностью, стабильным коэффициентом трения и высокой теплопроводностью. Благоприятным результатом воздействия алюминия на ростоустойчивость чугунов является смещение критических точек фазовых превращений в область высоких температур. Это обстоятельство имеет особенно важное значение при работе отливок в условиях циклических нагрузок. При термоциклическом воздействии в области температур фазовых превращений может происходить неравномерное попеременное расширение и сжатие под влиянием изменений большой разницы удельных объемов образующихся фаз. Все это способствует образованию трещин и, в конечном итоге, вызывает рост, а затем и разрушение литых деталей.
В структуре алюминиевых чугунов всегда находится определенное количество различных соединений, образуемых постоянными примесями сплава, например, сульфидов и фосфидов. Относительно высокая гетерогенность строения алюминиевых чугунов создает заметные затруднения при установлении закономерностей, связывающих структуру со свойствами сплавов.
В сплавах с высоким содержанием углерода алюминий влияет как на процесс графитизации, так и на структуру металлической основы. Алюминий, как известно, способствует графитизации чугуна. Однако при увеличении содержания алюминия свыше 5 % его графитизирующая способность снижается, а при 9… 16 % сплав затвердевает без выделения графита. Чугун этой группы характеризуется высокой твердостью, хрупкостью и плохой обрабатываемостью. Дальнейшее повышение в чугуне содержания алюминия до 25 % снова приводит к интенсивной графитизации. Чугун, легированный 19…25 % алюминия, имеет вполне удовлетворительные литейные свойства. Часть алюминия может быть связана в нитриды. Этот легированный чугун может быть использован для изготовления зубчатых колес планетарных редукторов и деталей колодочного тормоза скребковых конвейеров и других тормозных устройств.
Свойства алюминиевых чугунов во многом определяются специфической структурой графита, который находится в виде коротких пластин со скругленными концами. Отливки из алюминиевых чугунов, изготовленные в песчаных формах, имеют более чистую поверхность, чем у отливок из обычного серого чугуна. Алюминиевый чугун отличается также повышенной коррозионной стойкостью вследствие образования на поверхности тонкого защитного слоя из окиси алюминия. При содержании алюминия свыше 26 % чугун становится очень твердым и хрупким.
Легирование чугунов нитридами и окислами алюминия сопровождается заметным изменением целого ряда характеристик отливок. Ввиду этого при выборе химического состава чугунов для изготовления изделий определенного назначения необходимо принимать во внимание весь комплекс физико-механических свойств.
Увеличение производства износостойких отливок из легированных чугунов сдерживается высокой стоимостью и дефицитностью присадок, повышающих фрикционные и физико-механические свойства. Поэтому для литейного производства представляют интерес отходы различных производств, осадки химического растворения кернов и отработанные катализаторы, содержащие оксиды алюминия, молибдена, никеля, марганца и других цветных металлов. При высоких перегревах доэвтектических Fe-Si-C-расплавов хорошо растворяются такие катализаторы, как ГО-17, содержащий 21…23 % (мас.) Мо03, 7… 12 % (мас.) NiO, остальное А1203. Также используется и АКМ, содержащий 10… 13 % (мас.) Мо03, 3…5 % (мас.) СаО, а остальное А1203. Наиболее приемлемым плавильным агрегатом для реализации такой технологии является дуговая печь, обеспечивающая формирование горячих жидкоподвижных шлаков.
При оценке фрикционных свойств легированных чугунов необходимо учитывать способность получаемых структур к изменениям в результате сложной совокупности процессов, происходящих при эксплуатации, а также направление и характер этих изменений в каждом конкретном случае. Можно отметить, что в стабильных структурах (улучшенных или нормализованных термообработкой) в процессе фрикционного износа возникают значительные остаточные напряжения, существенные изменения микрогеометрии поверхностей, снижающие эксплуатационную стойкость пар трения. Легированные фосфористые чугуны подвергают обработке в термических печах.
Представляет практический интерес влияние микролегирования на фрикционные свойства чугуна при удельных давлениях до 25 МПа и скоростях скольжения до 15,5 м/с.
Установлено, что скорость изнашивания образцов существенно увеличивается при достижении поверхностью контакта температуры 250… 300 °С при удельных контактных давлениях 18…20 МПа и скоростях скольжения от 1 до 15 м/с. В случаях развития явления схватывания высокая скорость изнашивания может иметь место и при более низких удельных давлениях, скоростях скольжения и при температуре более 180 °С.
Легирование фосфористых чугунов молибденом и никелем (при использовании термической обработки — улучшения или изотермической закалки отливок) сопровождается заметным повышением фрикционных свойств. Изотермически закаленные фосфористые чугуны имеют превосходство по износостойкости над чугунами, подвергнутыми закалке и отпуску. При одинаковой твердости они имеют меньший износ при сухом трении.
Высокую износостойкость фрикционным отливкам обеспечивает ниобий. Преимущество ниобия состоит в том, что он в отличие от хрома и молибдена не увеличивает склонность чугуна к отбелу. Образцы из чугуна, содержащего 0,6…0,7 % ниобия и 0,15 % фосфора, обладают временным сопротивлением 370…453 МПа, а износ их не превышает 30 мг/гс при нагрузках 15,5 МПа и скорости скольжения 12 м/с. Они отличаются стабильностью коэффициента трения при температуре до 600 °С. Термическая стойкость такого чугуна — 210.. .280 циклов.
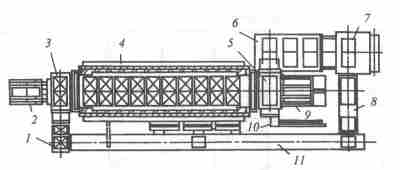
На рисунке приведены данные о влиянии кремния, молибдена и никеля на износ чугуна, содержащего 0,12…0,15 % фосфора. Снижение износостойкости чугуна при увеличении содержания кремния связано с появлением в структуре отливок значительного количества ферритной составляющей. Это снижение износостойкости отмечается и при наличии в фосфористых чугунах таких микролегирующих элементов, как кальций и алюминий. Величина износа меняется и зависит не только от степени легированности чугуна тем или иным металлом или их комплексами, но и от толщины стенок отливок и содержания технологических примесей в расплаве.
Изотермически закаленные чугуны с успехом заменяют стали и используются для таких деталей, как зубчатые колеса заднего моста автомобилей, буксы и входные валы-шестерни коробки передач.
Технологический процесс изотермической закалки включает следующие операции: аустенизацию, охлаждение до температуры изотермического превращения, выдержку при этой температуре и охлаждение до комнатной температуры. Аустенизация проводится при температурах 870…910 °С в печах безокислительного нагрева, а температура изотермического превращения может колебаться в пределах от 300 до 680 °С.
В практике производства износостойких отливок используются в основном две группы изотермически закаленных чугунов: с мелкозернистой структурой продуктов промежуточного превращения, мартенситной или структурой остаточного аустенита.
Изотермически закаленные чугуны с мартенситной структурой имеют более высокое временное сопротивление (900… 1500 МПа), хорошую износостойкость и относительное удлинение 2…5 %. Чугуны, закаленные при температурах 300…350 °С и содержащие в структуре 5…20 % остаточного аустенита, обладают более низким расчетным сопротивлением 500…700 МПа, но высокими пластическими свойствами (относительное удлинение достигает 7… 14 %), хорошей обрабатываемостью и термической стойкостью. При изменении температур изотермической закалки в износостойких отливках можно получить широкий спектр структур (сорбит, троостит, бейнит, зернистый перлит, мартенсит, остаточный аустенит) и физико-механических свойств. Износостойкость изотермически закаленного чугуна со структурой бейнита и остаточного аустенита является наиболее высокой.
Для получения игольчатой структуры наиболее эффективно легировать серый чугун молибденом, который способствует стабилизации структуры и свойств чугуна в отливках. Более экономичными легирующими компонентами серого чугуна являются ванадий и медь. Могут использоваться ферроникель, феррофосфор, олово и другие компоненты.
Влияние микролегирования на величину среднего износа серого износостойкого чугуна, содержащего 0,15 % фосфора, показано на рисунке. Олово, вольфрам, молибден, ванадий, бор и медь значительно повышают износостойкость чугуна уже при содержании этих элементов более 0,4 %. Более сильное влияние на свойства чугуна они оказывают при совместном введении в расплав.
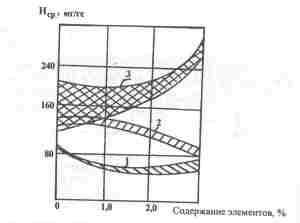
Отливки из чугуна с игольчатой (мартенситно-бейнитной) структурой обладают наиболее высокими фрикционными и эксплуатационными свойствами и могут использоваться и для других тяжелонагруженных литых деталей.
Установлено, что присадка 1 % меди и 0,1 % сурьмы увеличивает ав низколегированного серого чугуна на 12… 16 % и твердость на 18…27 НВ. С повышением углеродного эквивалента чугуна влияние микролегирования на кристаллизацию графита уменьшается. Упругопластические свойства при увеличении концентрации сурьмы от 0,002 до 0,2 % (мас.) уменьшаются на 12…26 %. Медь в таких количествах на упругопластические свойства заметного влияния не оказывает.
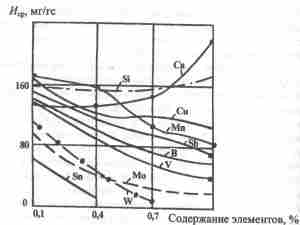
Комплексно-легированные чугуны с игольчатой структурой могут использоваться для изготовления деталей подвижного состава. Эти отливки имеют массу от 6,6 до 15 кг и являются ответственной частью системы подвески, работающей в сложных условиях фрикционнодинамического нагружения. В зависимости от скорости движения, нагрузок и состояния рельсового пути характер силового взаимодействия вагонов и колес непрерывно изменяется, поэтому в фрикционных узлах постоянно имеют место скольжение с качением, резкие продольные и поперечные перемещения.
Для повышенной динамической прочности содержание молибдена в чугуне повышается до 0,8… 1,0 % и меди до 1,3… 1,7 %, а содержание фосфора снижается до 0,06…0,15 %; временное сопротивление такого чугуна — 350.. .450 МПа.